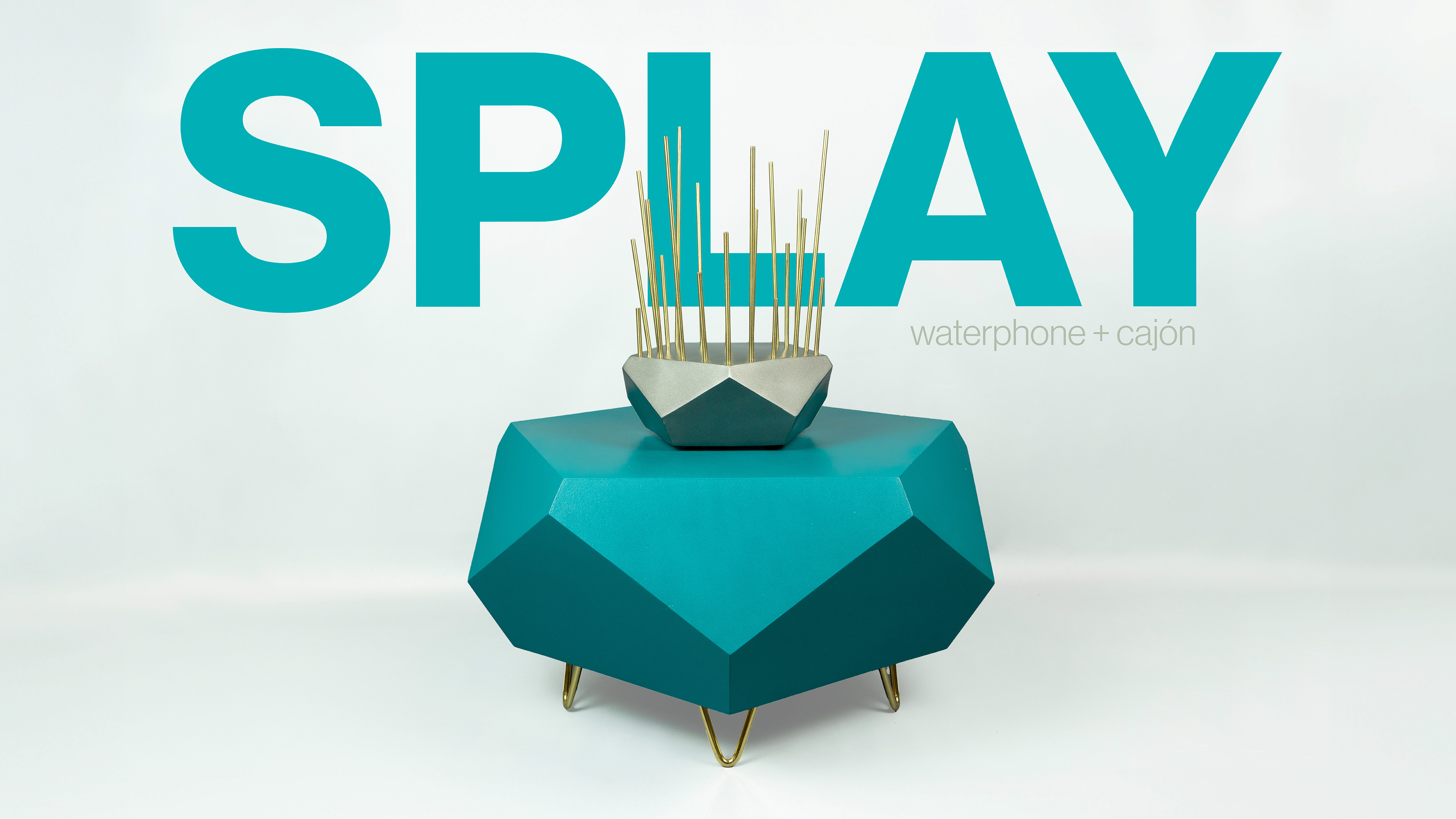
Splay was a 7 week long project, completed in my Fall semester of my Junior year at JMU for a Percussion Design class. The design brief being to create a novel percussive instrument while innovating the form and function.

Splay is a collection of percussion instruments; a waterphone and cajon, that have been designed not only to produce great sound, but also serve as elegant works of sculpture and fine furniture.


My main inspiration for this project came in researching the classic waterphone and cajon, and seeing how and where I could make improvements. I set out to make the form of both instruments more visually interesting, and at the same time I was trying to improve the sound and functionality of the two. An advantage I had going into this project was that I had already designed two sets of cajons previously. I knew for this project, I wanted to turn the traditionally one sided cajon into one with numerous sides, while also making it a functional furniture piece. Looking at geometric metal forms for inspiration, I envisioned a twelve sided form that could work for both the waterphone and cajon. In doing so, the waterphone would be enhanced visually, while the cajon would be enhanced not only visually, but also in its function as a box drum.
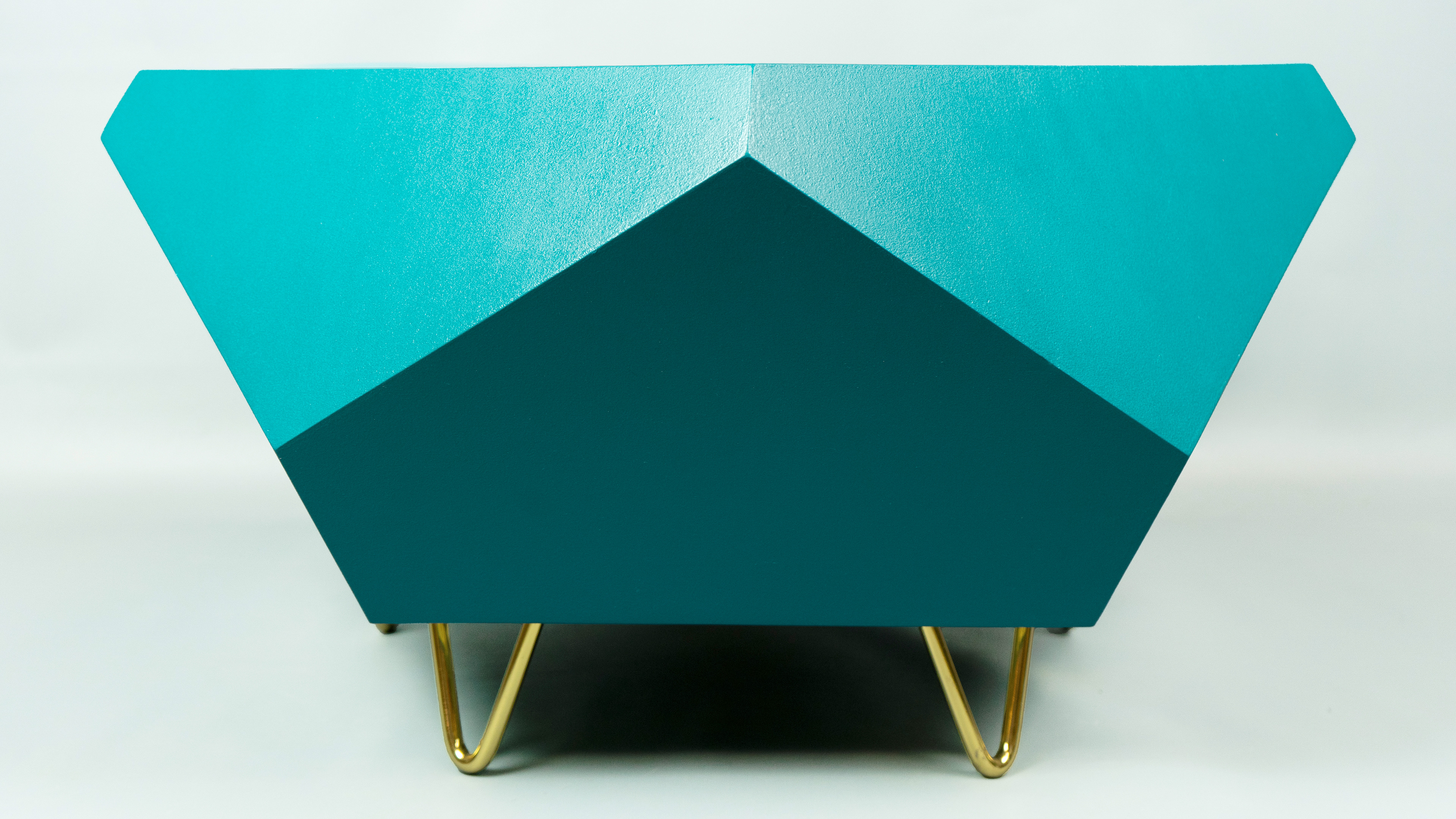
This altered dodecahedron shape allowed for 11 different hitting surfaces (10 on the sides, 1 on the top) at 3 different angles. Each hitting surface, because of the different shape and angle, produces its own unique sound while being played.
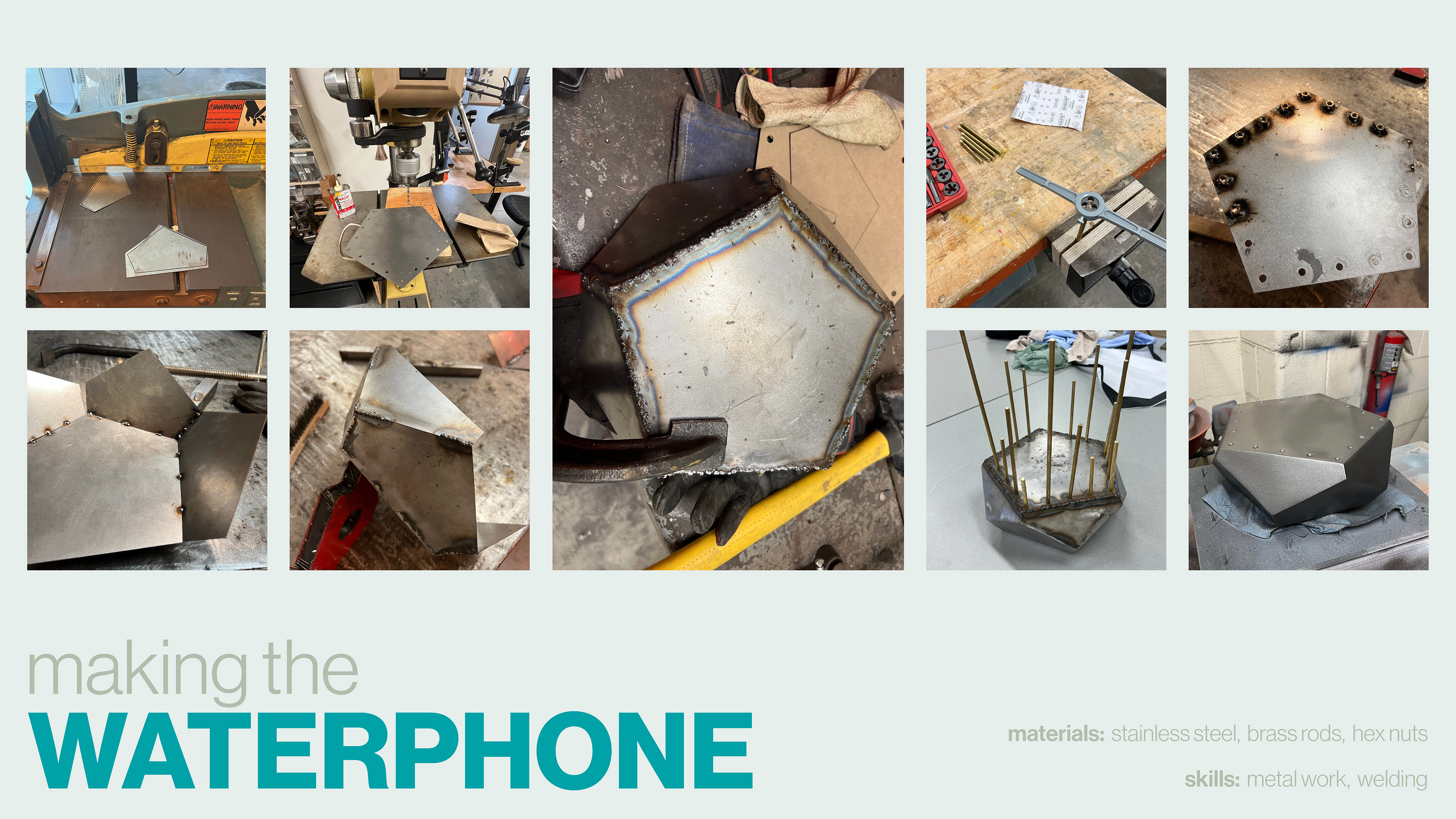
The making process for the waterphone was a new one for me. I was ambitious for designing a multifaceted bowl that I knew I needed to weld together, but my lack of welding knowledge did not stop me. I learned through different tests what settings and processes would give me the best welds, and eventually the whole bowl came together. Instead of welding the rods onto the bowl like a traditional waterphone, in order to allow for a maneuverable rod, I tapped and threaded them into the bowl. This allows the user to change the order of the different size rods, to change the pitch and sounds the waterphone makes while playing. Then, after lots of grinding and sanding, I painted the bowl to finish it off. The updated form enhances the waterphone visually, and the maneuverable rods enhance the instrument functionally.
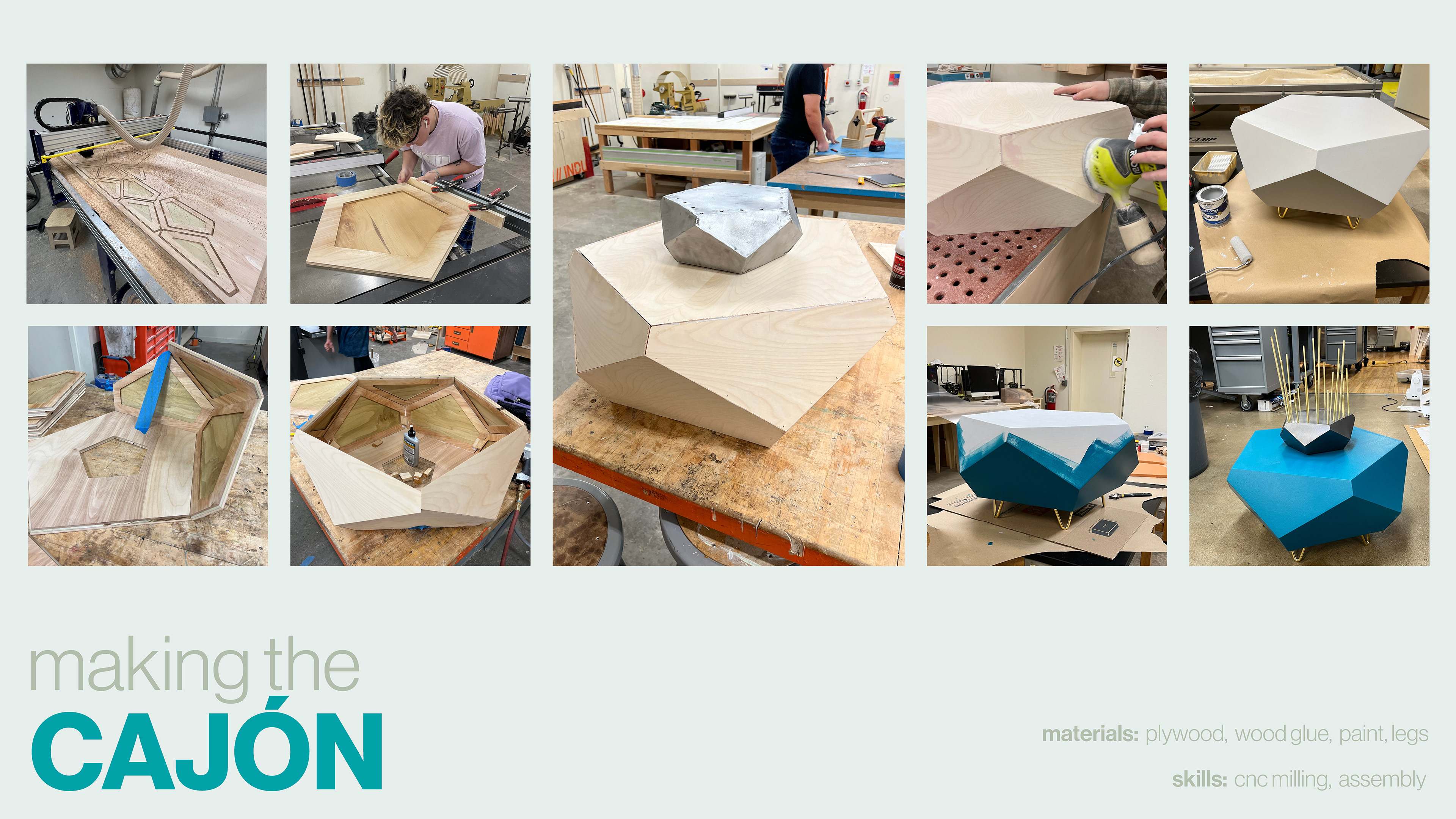
The cajon process was one I was more familiar with, however, it did come with its challenges. The 12 pieces were cut out of 3/4" plywood on the CNC machine, as well as a pocket to semi-hollow out the faces in order to create a thinner hitting face of the drum. Each of these pieces needed angles cut on all sides in order for them to fit together into the dodecahedron shape; I did this on the table saw. I then glued and nailed all of the pieces together. After sanding and painting, the cajon was finished. Not only does this cajon make a great loud sound when hit, but it also serves as a stylish modern ottoman or side table when not in use.
