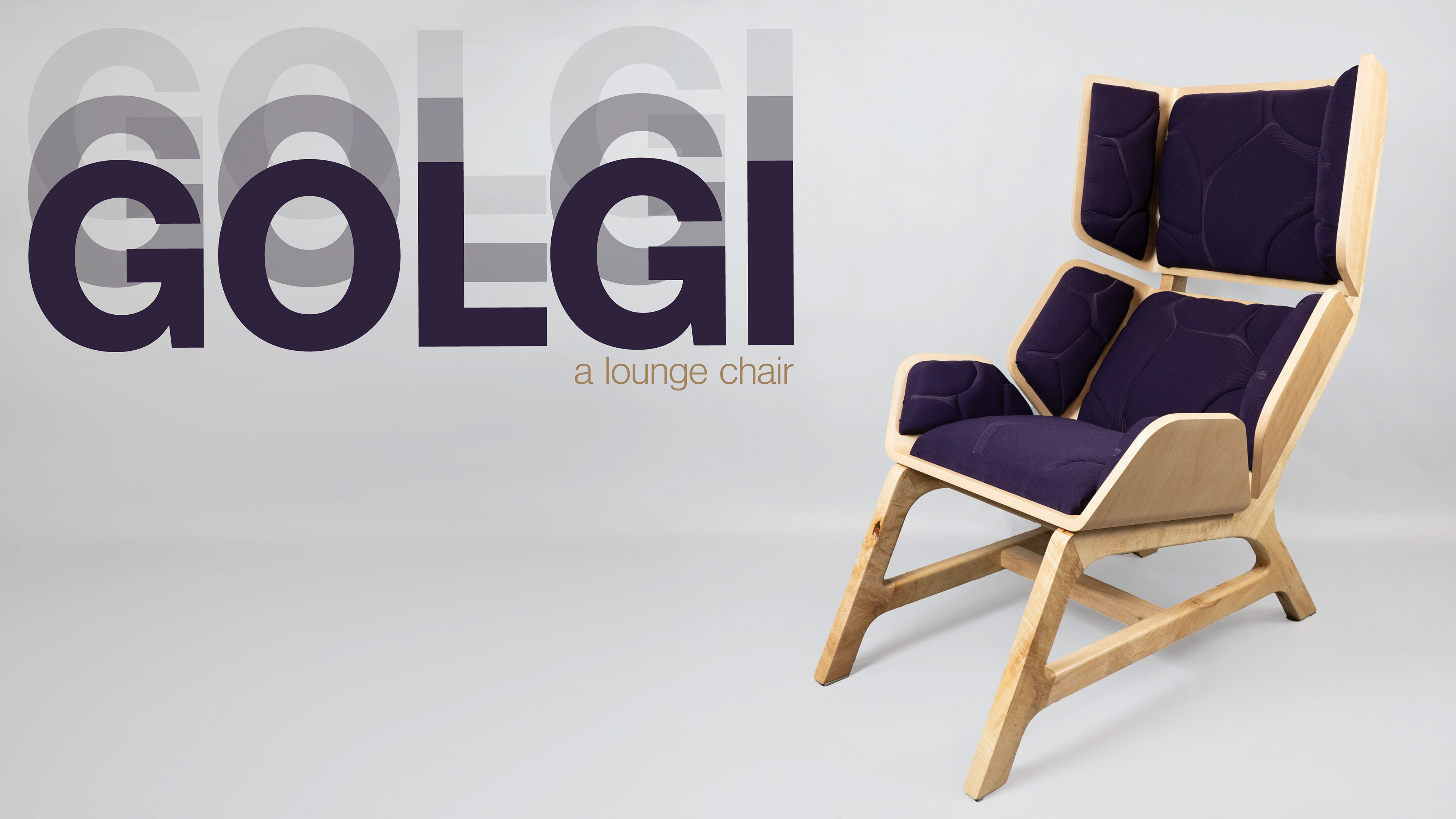
Golgi was a 5 week long project, completed in my Spring semester of my Junior year at JMU for a Computational Design class. The design brief being to design a piece of furniture for the modern household, using aspects of parametric design.
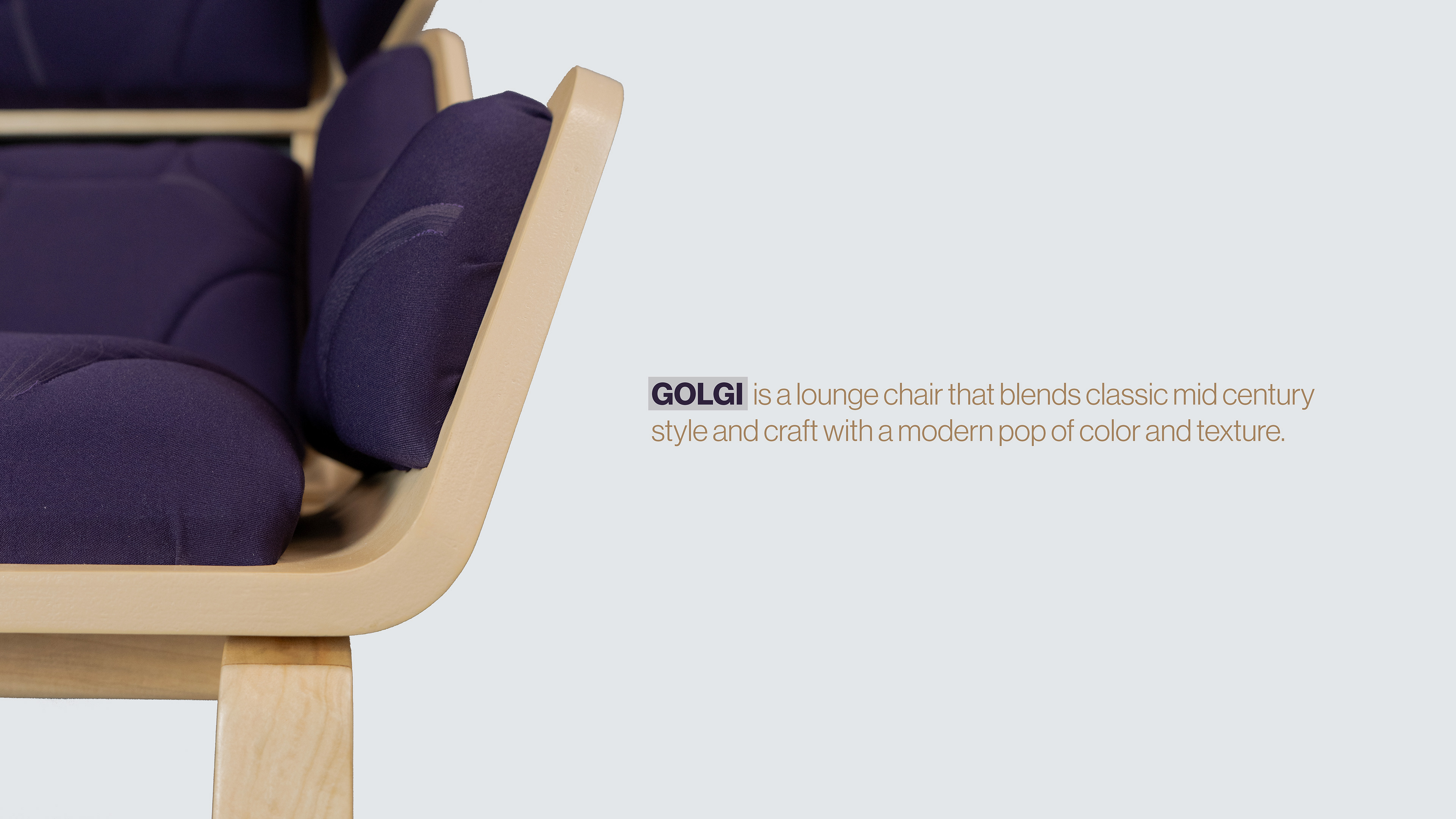
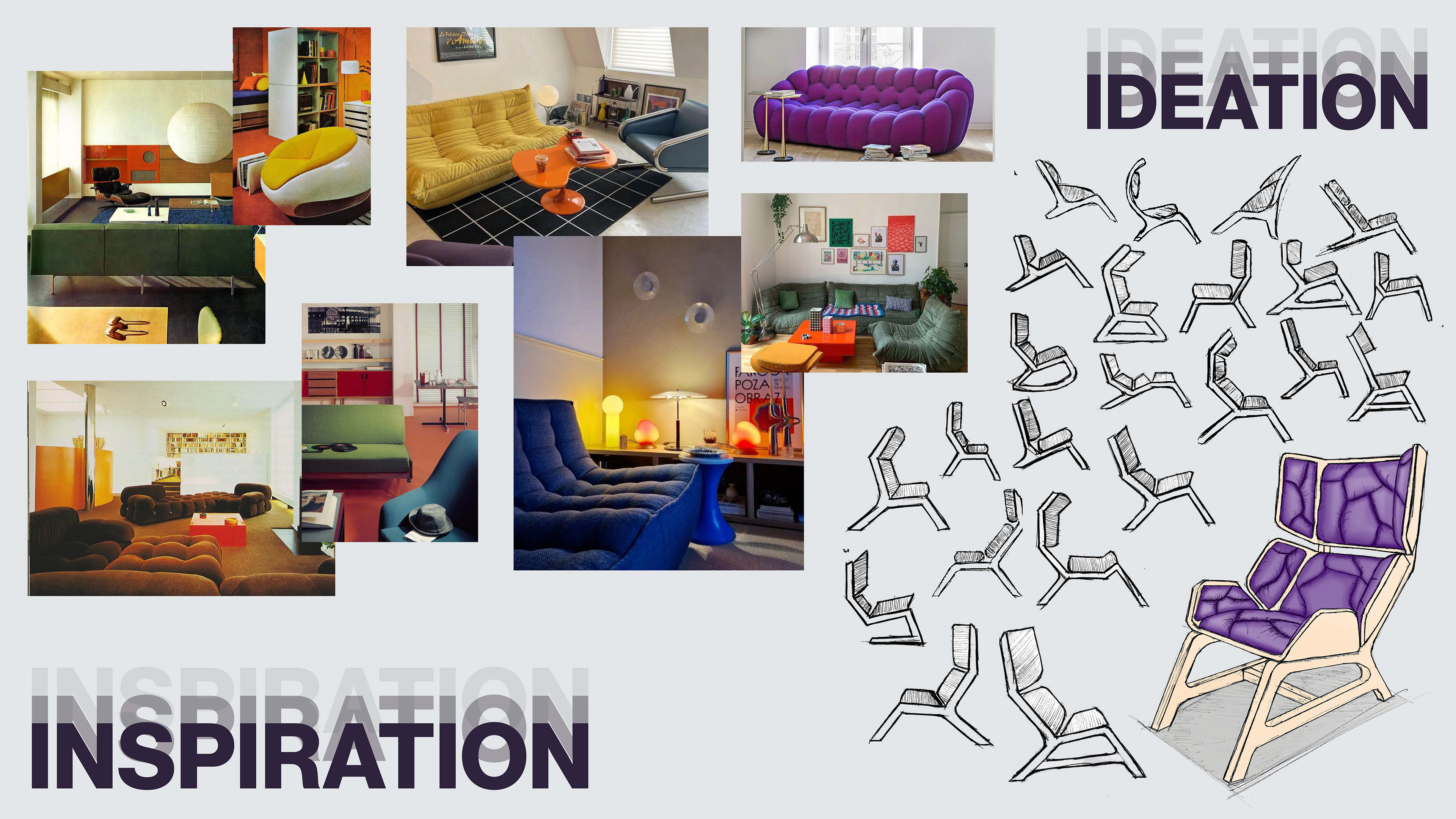
I've always been inspired by the vibes and aesthetics that 50's and 60's furniture and interior design give off, most notably, the Eames Lounge Chair. For this project, I wanted to blend those aesthetics with that of modern day furniture and interiors, especially the Bubble Sofa by Sacha Lakic. In doing so, I began sketching side profiles of chairs that could have elegant wood features, along with a pop of color and texture in the cushions. Eventually landing on the final design of Golgi.
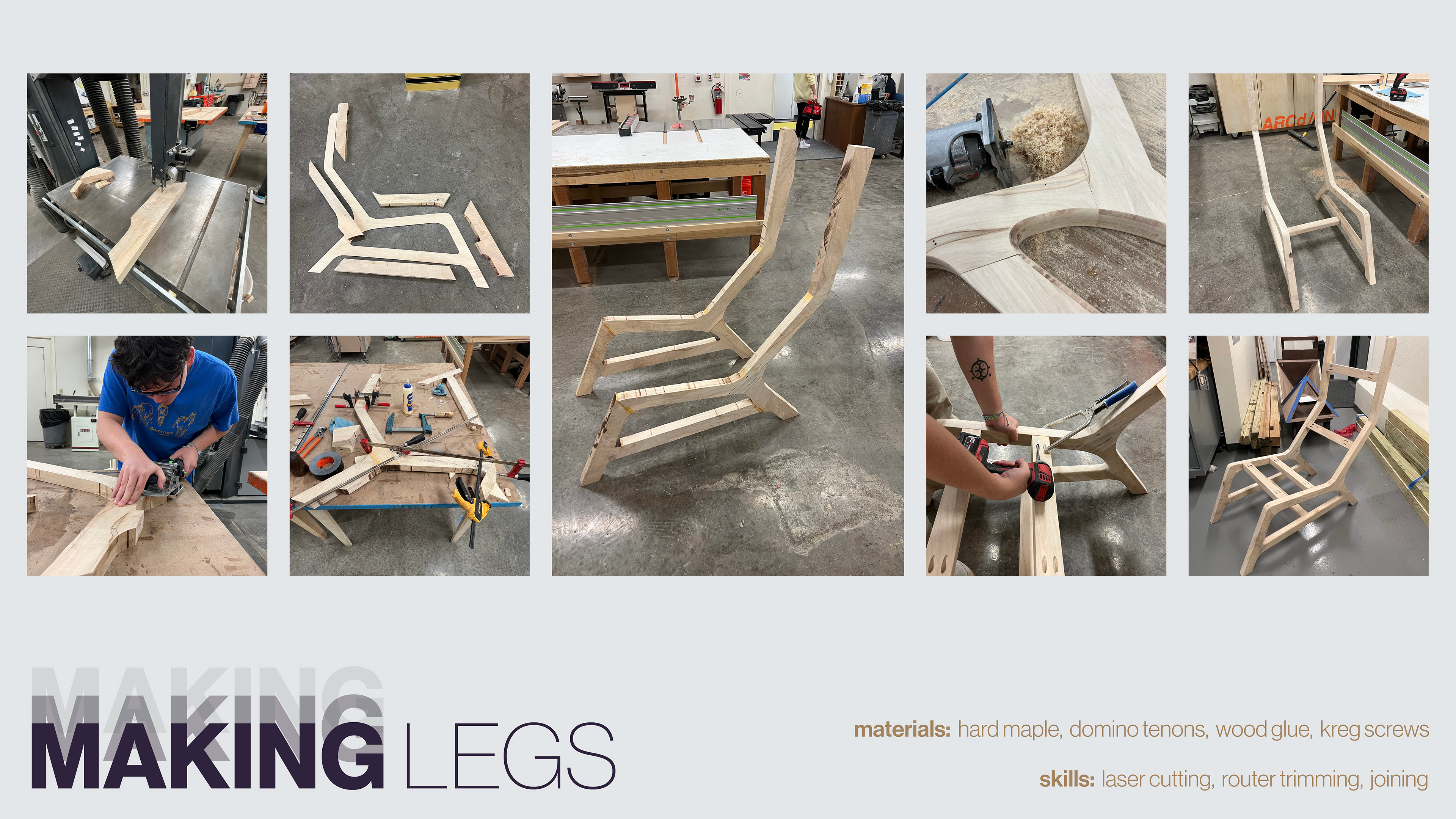
The making process for the final prototype of Golgi was a very crammed 14 days. I started with the legs, first by milling up 2" thick locally grown hard maple down to 1-3/4". I then cut out the 12 pieces that would make up the legs, before gluing and Domino joining them together. I then used a CNC cut template of the leg profile to flush trim the legs to final size using a hand router. After routing a roundover on all the edges, and sanding, I screwed the two sets of legs together with cross members.
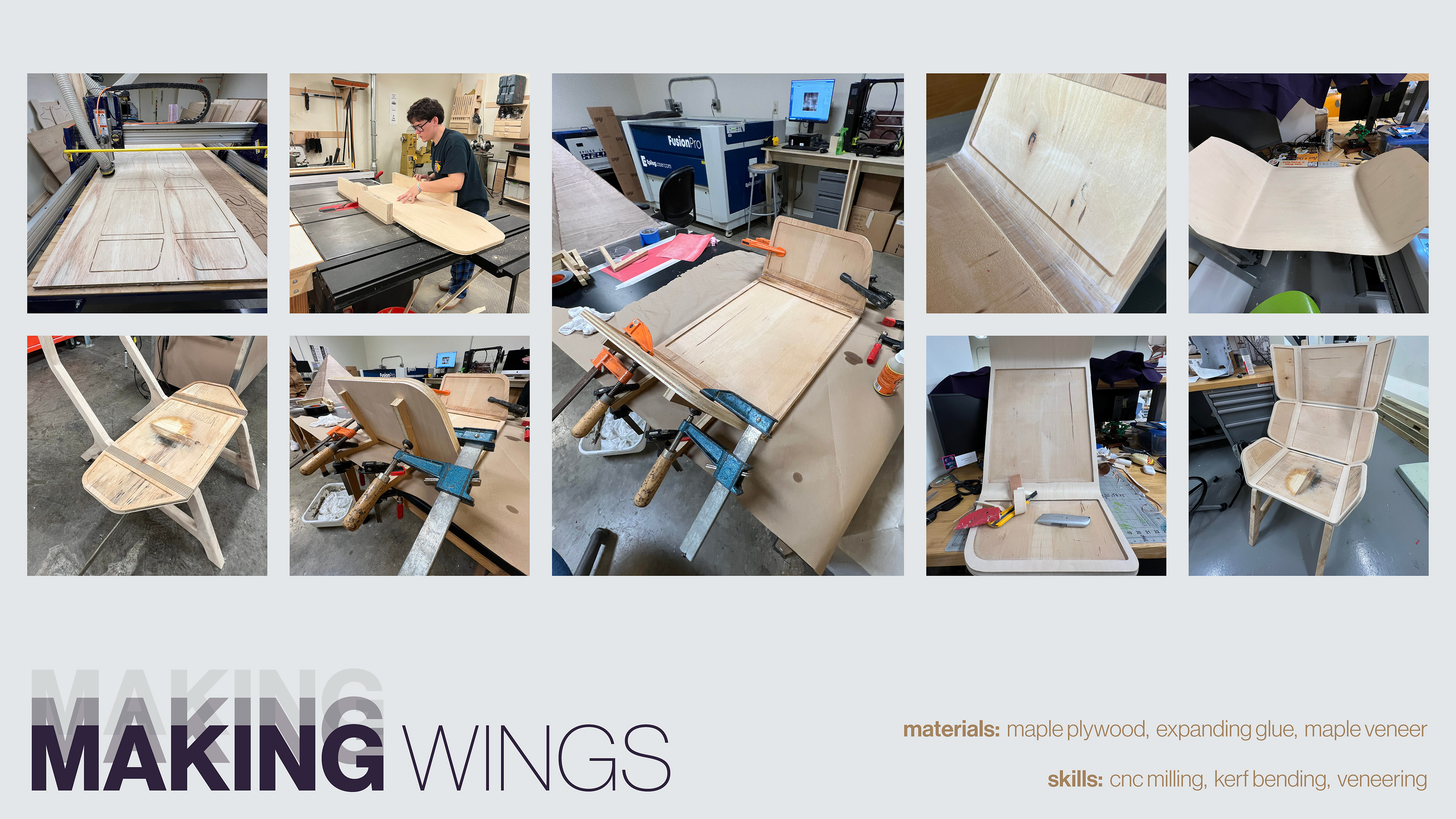
The next step in the process was making the panels or wings of the chair. Using 3/4" maple plywood, I started by cutting out the shapes as well as the cushion pockets on the CNC router. To make the bends in the wings, I cut kerfs against the grain of the wood. Then using angled clamping jigs, I glued the bends into place with expanding glue. Once dry, I sanded the inside curve smooth and veneered the inside of the wing. To finish the wings, I trimmed the veneer where the cushions would be inset, sanded the edges, then edge banded to finish it off.
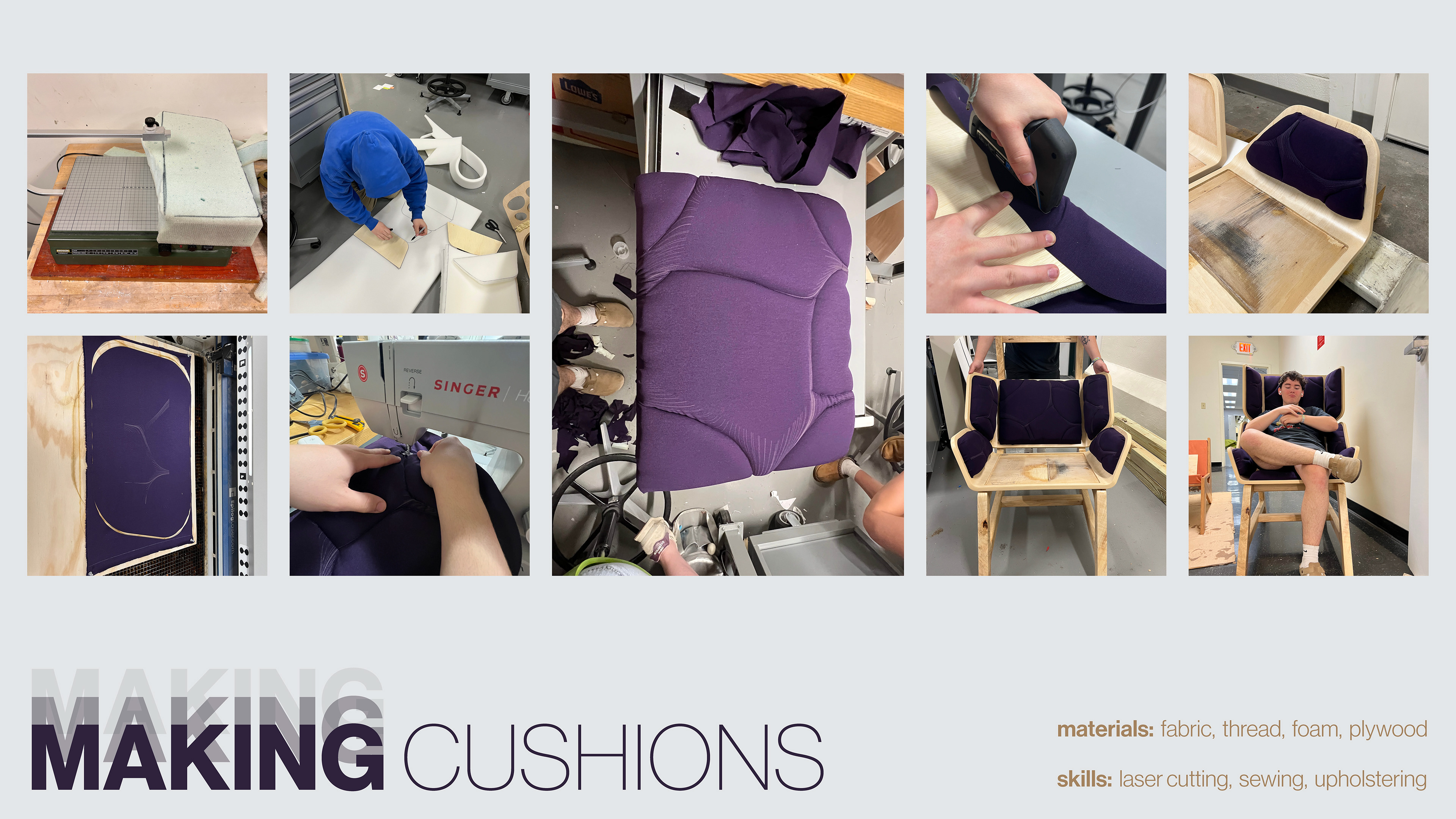
The last part to finish the chair was the cushions. To begin, I used Grasshopper, within the CAD modeling program, Rhino, in order to create a parametric pattern. This pattern could be infinitely changed, meaning each of the nine cushions on the chair could be different. I then laser etched this pattern on the fabric, as well as cut out the shapes of the cushions. To create a tufted look, I sewed the fabric through a 1" thick foam along the pattern lines, which was then upholstered onto a thicker 2-1/2" foam and stapled onto a 1/4" piece of plywood. These individual cushions are then pressure fit into the pockets of the wings.
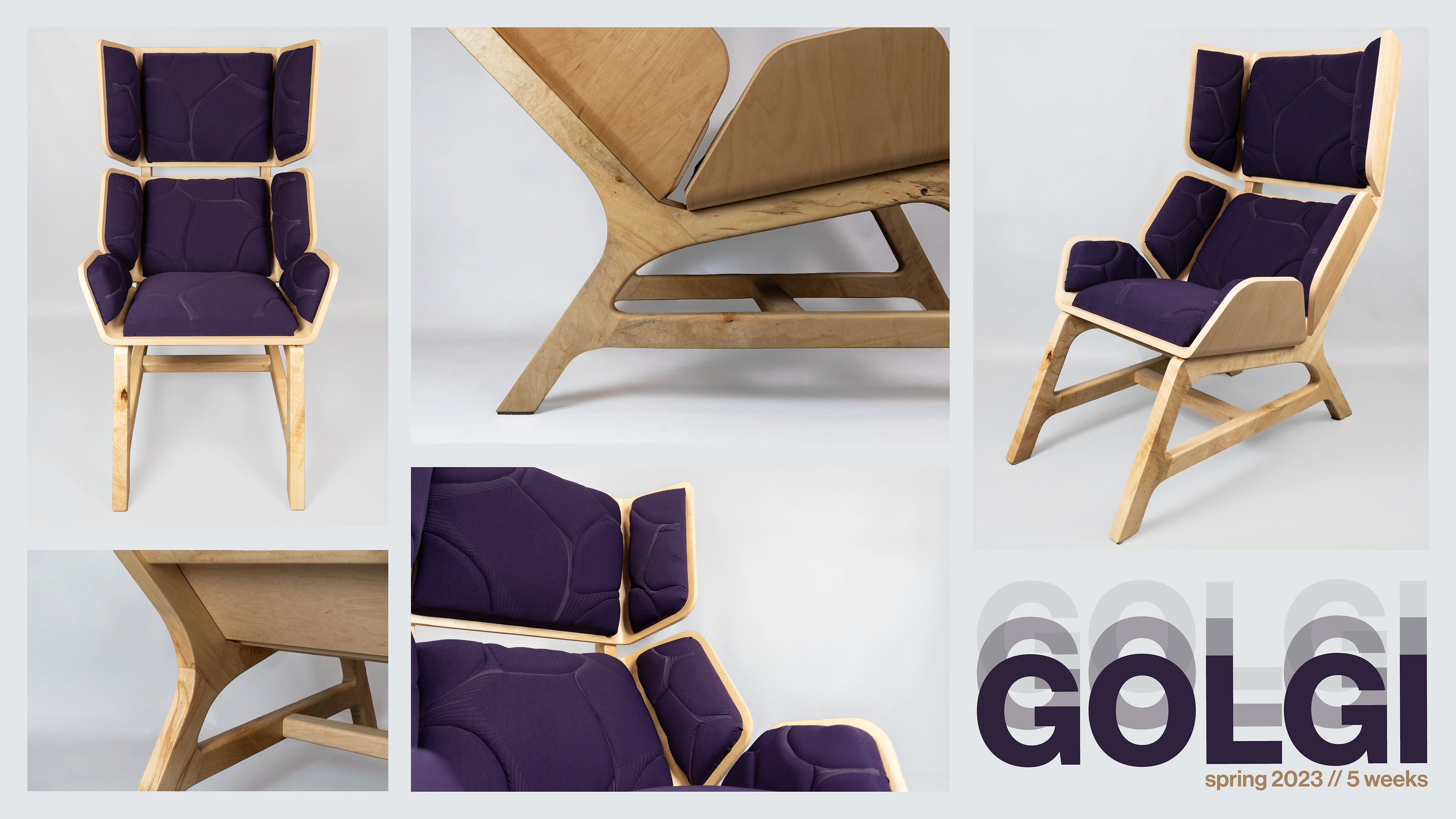